From simple to complex parts we provide accurate and precise milling of parts with vertical and horizontal machines. CEM will work with you to make prototypes, finish low run jobs, or meet demands for high volume needs.
Horizontal CNC milling
CEM’s horizontal milling operations are particularly effective for producing parts with complex shapes, heavy-duty operations, and multi-axis machining requirements. The horizontal orientation of the spindle provides excellent stability, precision, and access to different sides of a workpiece, making it ideal for certain types of products.
Here are some products that are best suited for horizontal CNC milling:
1. Large, Heavy, or Thick Parts
-
Structural Components: Heavy-duty machine parts like frames, bases, and structural elements.
-
Automotive Chassis: Parts like engine blocks, transmission housings, and large frame components.
-
Aerospace Parts: Large structural elements for aircraft, such as wing brackets, fuselage components, and engine parts.
-
Mining Equipment Parts: Durable parts for heavy machinery, such as drill heads and crusher components.
2. Complex Geometries & Multi-Sided Machining
-
Mold and Die Components: Molds for plastic injection molding or die-casting processes. Horizontal CNC milling can machine multi-sided molds in a single setup, reducing the need for repositioning.
-
Turbine Blades: Complex shapes requiring high precision and multi-axis machining. Horizontal milling is well-suited for making turbine blades used in power generation and aerospace.
-
Tooling & Fixtures: Custom jigs, fixtures, and tool holders that require high precision and detailed geometry.
3. High-Volume Production Parts
-
Automotive Engine Components: Parts like cylinder heads, crankshafts, and camshafts, which require high repeatability.
-
Brackets & Mounting Plates: Components used in machines, vehicles, or industrial equipment that need to be produced in large quantities.
-
Pump & Valve Bodies: Parts used in industrial and automotive applications that require consistent machining for tight tolerances.
4. Parts with Complex Features
-
Gears & Gearboxes: Gears that require multiple precision cuts and machining from various angles.
-
Precision Bearings: Machine components like ball bearings, shaft housings, and precision bearing assemblies.
-
Aircraft Landing Gear Components: These components have intricate features that need to be machined with tight tolerances.
5. High-Tolerance Components
-
Medical Device Components: Parts like surgical tools, implant components, or precision surgical guides, which require extremely high levels of accuracy.
-
Electronic Enclosures: Metal enclosures or housings for sensitive electronics, which require precise cuts and designs for wiring or mounting purposes.
6. Parts with Multi-Axis Machining Needs
-
Rotary and Cylindrical Parts: Parts like shafts, cam mechanisms, and rotary parts that require machining from different angles.
-
Heavy-Cut Components: Large, thick metal parts requiring multiple passes and efficient chip removal, such as in metalworking and fabrication.
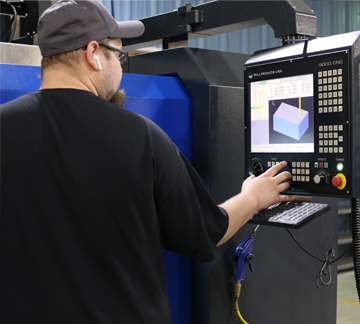
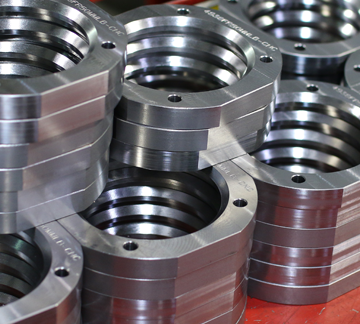
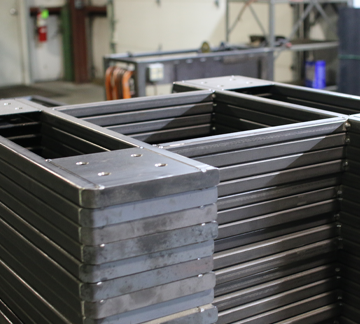
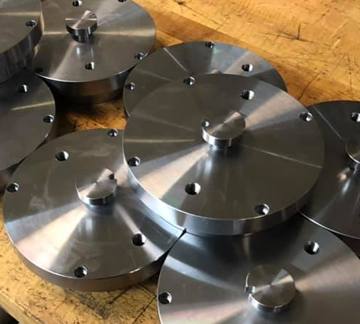
Our Quality Pledge
We pledge to deliver products and services that meet or exceed customer requirements, uphold CEM’s high standards, and ensure exceptional safety, performance, and reliability.
Commitment To Quality Goal
To drive a culture of excellence by embedding quality, safety, and reliability into every process and product, ensuring that CEM consistently exceeds customer expectations and industry standards
Furthermore, CEM is deeply committed to client satisfaction and profitable operations, achieved through continual improvement and employee ownership of all programs and projects. We hold ourselves to ever-increasing standards of excellence in everything we do, recognizing that satisfying client requirements is crucial to our continued success and a key reason behind our high customer retention and repeat business.
Our processes are designed to begin by clearly defining the client’s requirements, followed by a thorough review to ensure that these requirements have been fully met. Importantly, everyone involved in providing products or services to our clients takes ownership of ensuring that the client’s needs are well-defined, well-documented, and that the final products or services fully meet the specified requirements.
Industry Specific Needs and Materials
As a trusted partner to customers large and small, we have become experts in working with materials used across our focus industries
Why Horizontal CNC Milling?
Horizontal CNC milling is ideal for these products due to:
-
Better Chip Removal: The horizontal position of the spindle ensures gravity helps remove chips more effectively, preventing buildup and clogging.
-
Multiple-Side Machining: Horizontal mills allow for workpieces to be loaded and machined on multiple sides without re-fixturing, saving time and improving precision.
-
Stability for Larger Parts: The horizontal configuration offers greater stability when machining heavy or large parts, ensuring superior accuracy.
CNC Materials | |
---|---|
Metals | |
Aluminum | |
Copper | |
Bronze | |
Brass | |
Steel (Stainless Steel) | |
Plastics | |
Delrin | |
UHMW | |
Micarta | |
Nylon | |
HDPE |